Sacramento Warehouse Fundamentals Explained
Wiki Article
The smart Trick of Sacramento Cross Dock That Nobody is Talking About
Table of ContentsAbout Crossdock Warehouse4 Simple Techniques For Crossdock WarehouseThe Only Guide for Sacramento Crossdock WarehousingCrossdock Warehouse Fundamentals ExplainedAbout Sacramento Crossdock Warehousing
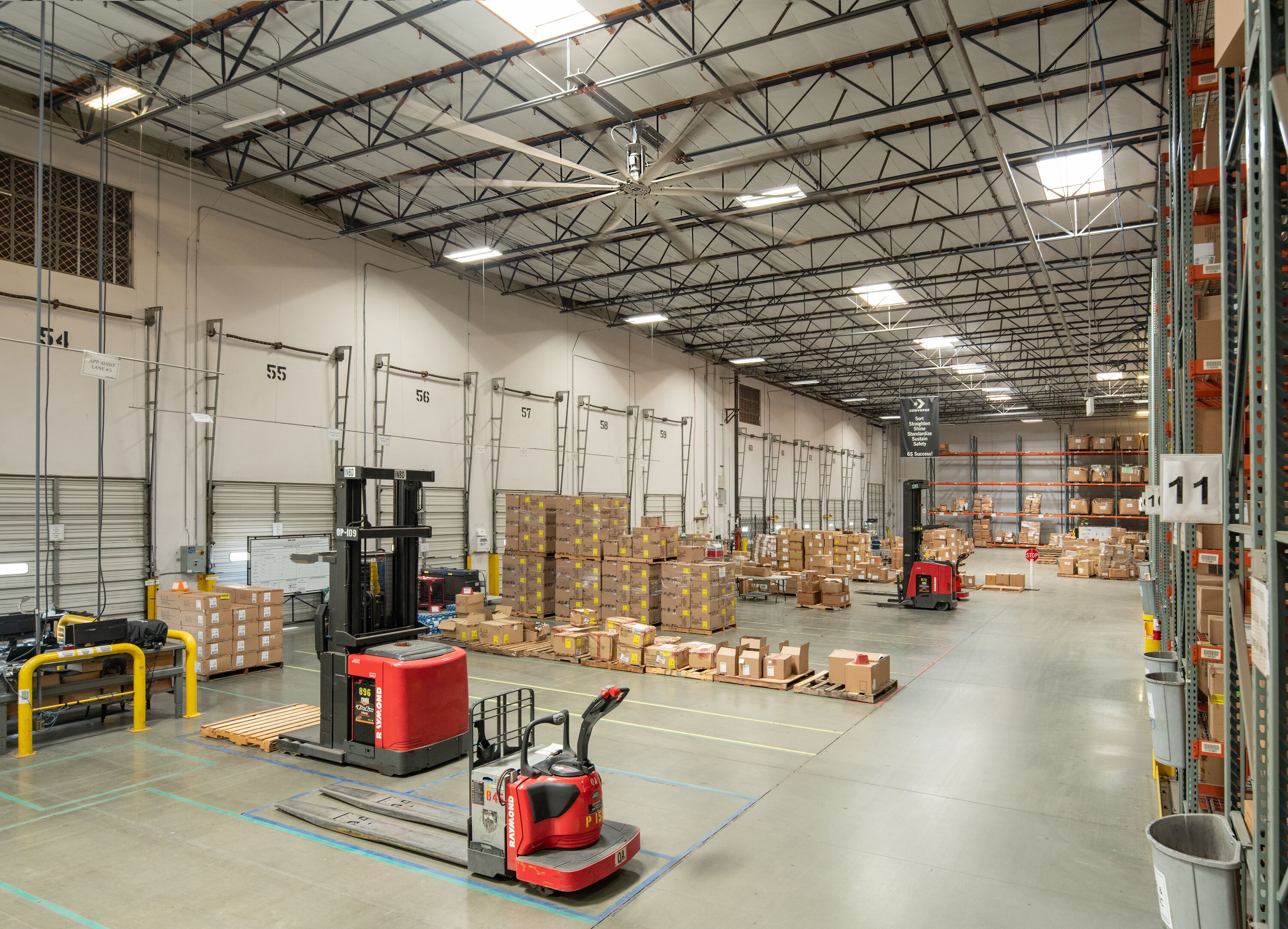
As a part of SCM, reliable inventory management may lead to a more powerful supply chain. Another reason excellent warehousing is vital to SCM is that it provides a means for services to make certain the availability of the best items at the right place whenever the time is. It enhances the energy worth of the products in this way - Sacramento Cross Dock.
Of course, they become a lot more hesitant when unpredictability exists around the prompt shipment of products. Nowadays, delivery speed appears to be one of the considerable aspects that consumers consider when choosing a product as well as determining whether or not to proceed with the purchase.
6 Simple Techniques For Crossdock Warehouse
A substantial factor to purchase developing a storage facility is the lots of recognized financial benefits that include it. Not only the boosted effectiveness of the supply chain yet also the stockroom's storage space ability as well as how it functions as a central area for your products add to its economic benefits.These things can be seen or realised with consolidation and also accumulation operations. Right here's a more detailed consider just how consolidation and also accumulation might aid lower prices: With debt consolidation operations, there's no demand to ship products separately from several sources because they could be supplied to your stockroom as supplies. As soon as an order is placed, you or your personnel can pack and deliver the product out from there.
Not just that, but great warehousing additionally improves client service and provides economic benefits. All of these things might cause greater earnings and improved service success.
Our Crossdock Warehouse PDFs
Individuals that load products into a stockroom as well as others ("pickers") who load orders in a true circulation center, plus those that take care of the facility and also procedure. Accessibility to cost-effective transportation to bring products in or move them out as orders are satisfied.They additionally need to guarantee that products are saved in a safe and safe manner. In retail shops, items are kept and also organized in a warehouse and delivered to consumers or other shops.
Warehousing best practice is to use RF Scanners, or equivalent innovations, to additional improve stock accuracy and also real time inventory monitoring. Closely linked with Getting, Putaway is the final phase of inbound handling. Putaway is the procedure of physically, and also systematically, placing items right into their proper final storage space places (Sacramento Cross Dock). Team chooses Product to putaway from Putaway Staging area, Usually Pallets or Carts with Item ready to be putaway, Making use of RF Scanner, recognize what cart/pallet/job you are putting away as well as scan one-of-a-kind identifier to start Putaway, Picker takes a trip to place to position item for storage, Ideal finest in course systems tell team where to put item, however lots of warehouses still have staff area item where they know there is empty room (with some requirements applied)RF Scan Product being putaway and Area where the Item is putaway, Continue procedure (go to location and also place supply) up until whole order, pallet, cart, and so on is Get More Info full Weight and also measurements of product/pallet being putaway, Stowability of Product (ie delicate, stackable, etc)Transaction quantity (HOT items placed close vs NOT much away)Quantity received, Worth of product, Select Kind of Product (single choice, set choice, cluster pick, area pick, etc) Accurate Putaway is critical in the stockroom procedure, making sure that Product can be conveniently located exactly when it is needed.
The Ultimate Guide To Crossdock Warehouse

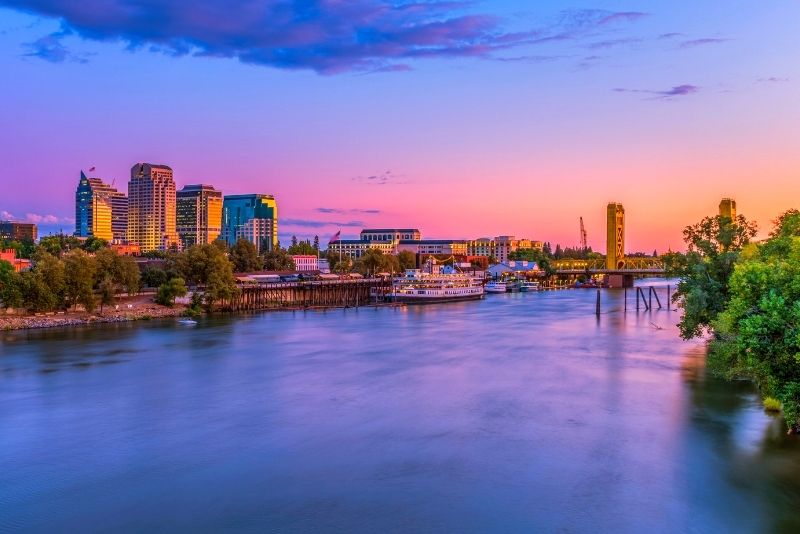
Choosing is the process of gathering Products to accomplish a customer's order request. Picker is appointed Pick(s)There are several choose techniques, each operation is special in what is most efficient for their demands, Zone selecting, batch picking, solitary read order picking, wave selecting, and also a lot more, Using RF Scanner, or similar, begin selecting by going into the One-of-a-kind Choose Identifier (set #, Order #, SO #, Pick #, various other reference)Picker is transmitted through the Choose Course (ideally based on optimization reasoning) to fulfill the Select, scanning Products and Locations as they advance, Selected items might be positioned in totes, pallets, carts, shelf, and so on during pick, Totally picked orders delivered to following stage of process, Chosen orders might be delivered to a High quality Control location, Packing/Shipping location, or straight to outbound hosting (if choice to label operation) depending on operation Limitations/abilities of present Stockroom Administration System (WMS)Quantity of Orders # of Item Lines per Order, Kind of storage space media (shelving vs racking vs ground pallet storage space)What the Packaging as well as Delivery Refine looks like (very closely linked to Picking)Product require additional focus throughout packaging? Transport Management System (TMS) capable of providing delivery tags before products are selected?
If throughout shipping the weight is not within the defined tolerance array, then the individual will be triggered to take activity, Measurement tolerance check throughout Delivery, Similar to Weight tolerance based on system measurement information Packing and also Shipping is a significant emphasis of storehouses, as it typically ends up being a bottleneck considering that Order Handling Time should be as brief as possible to satisfy consumer expectations.
Do NOT sacrifice quality! It is necessary to note, relying on the storehouse operation Packaging might be integrated with the Selecting process. Supply Control is an essential component of all storage facility procedures. You can guarantee the stock at the stockroom is accurate and also current with a well defined Stock Control procedure.
The Basic Principles Of Crossdock Warehouse
Cycle Matters and Full Inventory Counts are tools linked with maintaining Inventory Control. Cycle Counts occur constantly while typical operations continue, but Complete basics Supply Counts happen periodically as well as call for all item motion to stop up until a full accurate matter is finished. Closure all supply activities, completing all Item Motions in the Warehouse (physically as well as systematically)Guarantee all inbound and also outgoing orders that have been physically processed, have additionally been refined in WMSBreak storehouse team right into teams to matter (occasionally 1 individual group alright)Teams are appointed areas to count Assign small-medium locations to count, then groups sign in for more locations as needed, Groups count designated areas, videotaping counts of item per place, Teams often making use of RF Scanners to tape-record counts, Or else have to do paper-based which is hard to attain a Blind Count, Group reports back once finished as well as receive next Count Job, After areas are Counted, the Manager/Lead reviews all Differences, Manager designates DIFFERENT Group to state the distressed Products and/or Locations, If second group counts same as first team, make stock change to match physical count.Report this wiki page